Сополимер-полиолы как эффективная добавка в смеси полиуретанов
Для улучшения физико-механических свойств Полиуретанов, Полиэфир полиолы можно наполнить дополнительными органическими соединениями для производства композиций, с помощью которых можно получать более прочные и жесткие вспененные полиуретановые материалы.
Наполненные Полиуретаны также характеризуются большим количеством открытых пор, что также положительно влияет на физико-механические свойства конечных изделий.Полимерные наполнители обычно формируются методом полимеризации внутри объема базового (наполняемого) полиола. Полимеризационный процесс может протекать по свободно-радикальному механизму, либо по пути поликонденсации. Таким образом мономеры наполнителя вводятся в виде дисперсии в объем полиола.
Для приготовления качественных дисперсий, диспергируемые частицы должны обладать способностью к пространственной стабилизации, то есть возможностью к предотвращению слипания частиц с последующим осаждением. В большинстве случаев, стабилизация обеспечивается внедрением молекул наполнителя в структуру полиола, вследствие такого процесса получается сополимер-полиол.
Все сополимер-полиолы можно разделить на две основные группы - полученные методом последовательного радикального присоединения и полученные поликонденсацией.
Сополимер полиолы. Радикальное полиприсоединение
В 1950х компанией ICI был впервые разработан метод пространственной стабилизации дисперсий в безводной среде с помощью радикальной полимеризации. В 1966 были представлены первые отчеты об использовании техники полимеризации для получения полимерной дисперсии в полиэфир-полиолах. Основные химические реакции, сопровождающие процесс радикальной полимеризации приведены ниже:
В начале, при распаде молекулы-инициатора выделяются свободные радикалы, например, как в реакции распада алифатического соединения азо-бис нитрила. Свободные радикалы реагируют с молекулами мономера, этот процесс получил название стадии наращивания цепи. На этом этапе происходит относительно быстрое превращение молекул мономера в высокомолекулярную цепь. Последовательная реакция роста цепи прекращается, когда два конца радикальной цепи реагируют не с мономером, а друг с другом. Данный процесс получил название процесса обрыва цепи.
Скорость реакции обрыва цепи падает с увеличением вязкости и, соответственно, среднего значения степени полимеризации системы. Дальнейшее увеличение приведенных параметров приводит к образованию вязких сверхнасыщенных полимерных сред и в некоторых случаях к образованию «сшитых» полимерных систем - системы, в которых полимерные молекулы связываются друг с другом поперечными связями с образованием относительно жесткой трехмерной пространственной структуры.
Для предотвращения чрезмерного увеличения степени полимеризации, к системе добавляют специальные вещества, способствующие развитию реакции переноса цепи. Агенты реакции переноса цепи представляют собой низкомолекулярные соединения, способные к быстрой диффузии внутри полимерной среды. Агенты переноса цепи, реагируя с развивающейся радикальной цепью обрывают ее с выделением нового свободного радикала, образующего новую полимерную цепь.
Существуют также агенты реакции обрыва цепи, останавливающие полимеризацию, без образования нового радикального центра. Такие агенты используются для замедления полимеризации, при увеличении концентрации полностью останавливающие ее.
Первые коммерчески успешные сополимер-полиолы были основаны на использовании акрилонитрила, как основного базового мономера-наполнителя. Такие дисперсии содержали 20% (масс.) полиакрилонитрила и характеризовались значениями вязкости в пределах 3000 – 5000 мПа*сек. Полученные продукты в дальнейшем использовались для производства литых высокоупругих полимерных пен.
Повышенная твердость, прочность, упрощение производственного процесса и улучшенная структура пор таких пен привела к их высокому коммерческому успеху и распространению на рынке. Внедрение полиакрилонитрила в структуру полиольных цепей было произведено путем отщепления атома водорода от молекулы полиола с образованием свободных радикалов, вступающих в химическое взаимодействие с окружающими молекулами акрилонитрила. Первый образцы были получены в растворах акрилонитрила с винилацетатом.
По мере того, как технология использования сополимерных продуктов на основе полиолов развивалась и начала применяться в других областях, например при производстве блочных строительных пен, недостатки использования структур на 100% состоящих из акрилонитрила стали очевидны. Среди них – обесцвечивание пенных полимерных блоков. Желание преодолеть недостатки в свойствах привело к развитию использования так называемых SAN – смесей стирол-акрилонитрилов в качестве мономерных реагентов в процессе получения полиольных сополимеров.
Процесс полимеризации начинается с загрузки базового полиола и мономеров встраимого наполнителя в реактор. На этой ранней стадии, реакционная смесь находится в гомогенном состоянии, образующийся полимер имеет упорядоченную разветвленную структуру, напоминающую рыбный скелет. Центральная цепь “позвоночник” состоит в основном из повторяющихся звеньев базового полиола, а ответвления “ребра” - присоединенные молекулы наполнителя.
В процессе наращивания массы, образуются сферические структуры, в центре которых содержатся сополимер-полиольные образования, а внешнюю оболочку составляют присоединенные поверностно активные молекулы-модификаторы, которые продолжают взаимодействовать с окружающими их молекулами среды полиола.
Такие сферические структуры называются “прото-частицами” и имеют свойства, напоминающие мицеллярные системы, которые образуются про добавлении некоторых видов ПАВ к воде. Эта стадия называется ядрообразующей и сопровождается изменением окраса реакционный среды от прозрачного к мутно-белому.
Основная реакции полимеризации с активным наращиванием средней молекулярной массе происходит в ядрах упомянутых прото-частиц. Полимеризация в ядрах идет по тем же законам, что и стандартный процесс объемной полимеризации и, соответсвенно, замедляется при увеличении вязкости. К моменту химического равновесия, частицы увеличиваются в размерах примерно в 10 раз (от 0.01-0.05 миркон до 0.3-0.5).
Конечный размер варьируется в зависимости от изначального количества введенных мономеров. Разброс значений размеров и молекулярных масс частиц при таком методе проведения полимеризации достаточно узок, что позволяет получать вещества со стабильными и предсказуемыми характеристиками.
Сополимер полиолы. Поликонденсация
Полиолы с дисперсией полимочевины (PHD).
Помимо реакции радикальной полимеризации, для получения сополимерных композиций на основе полиолов используют реакции поликонденсации. Первыми образцами таких композиций, полученных поликонденсационным методом, стали смеси полиола и полимочевины (поликарбамид) – PHD полиолы. PHD полиолы представляют собой дисперсию фрагментов мочевины (-NH-CO-NH-) в массе полиола. Примером таких соединений может послужить продукт реакции между диамином (гидразин) с диизоцианатом (толуол диизоцианат) в присутствии полиэфирполиола.
Процесс полимеризации и построение молекулы сополимера для таких соединений существенно отличается от свободно-радикального механизма. В процессе поликонденсации используются низкомолекулярные олигомерные формы диаминов и диизоцианатов, в присутствии простых полиэфиров с концевыми гидроксильными группами.
Взаимодействие полиола с диизоцианатом заметно медленнее диамид-диизоцианатной реакции, что приводит к снижению количества полиольных звеньев в конечной сополимерной макромолекуле. Во время поликонденсации, скорость реакции и конечный молекулярный вес сополимера ниже, чем при свободно-радикальном процессе. В результатом, образуются более крупные частицы и более широкое распределение средней молекулярной массы, относительно полимерных SAN полиолов.
Полиизоцианатные полиолы (PIPA). Дисперсии полиуретана.
Также существует отдельный вид сополимер-полиольных композиций, отличающихся от PHD полиолов тем, что вместо диспергированных частиц полимочевины используются продукты реакции изоцианата с алканоламином, например триэтаноламином – то есть диспергируются частицы полиуретанов. Для получения таких соединений, выбранный амин добавляют к базовому полиолу, а затем интенсивным смешением вводят, например, толуолдиизоцианат.
Ускоренная катализатором, например оловоорганическими веществами, данная реакция способна завершиться в течение нескольких минут. Основной отраслью применения полиизоцианатных полиолов (PIPA) является производство пенопластов.
Другие Статьи
Смотреть все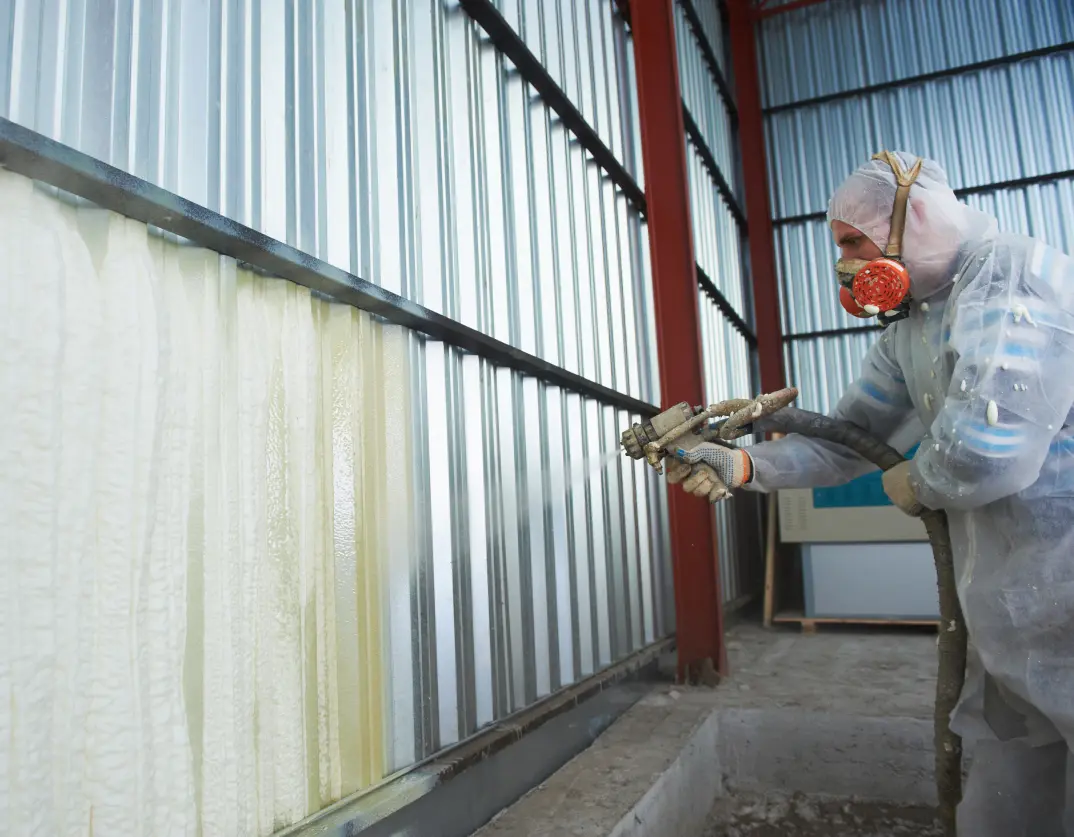